
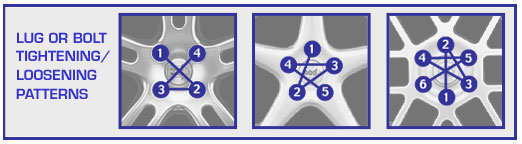
Proper installation requires torquing wheel-attaching hardware (lug nuts or bolts) to the recommended specification for the vehicle make, model and year. Torque specifications can be found in the vehicle's owner's manual, shop repair manual, industry reference guides or obtained from the vehicle dealer.
Proper torquing requires using the correct tools, procedures and patterns to prevent over-tightening hardware, stripping threads and stretching studs, as well as will reduce the possibility of warping brake drums, brake rotors or suspension hubs.
Under- or over-tightening wheel-attaching hardware can be damaging and dangerous.
Torque specifications are for threads free of dirt, grit, corrosion, etc., so the hardware turns freely. While lubricating hardware THREADS is recommended, it is important NOT to lubricate hardware SEATS. The friction which torque is measured against should come from the hardware seats. Lubricating hardware seats can result in inaccurate torque readings and/or over-torquing the hardware.
Professional recommends starting hardware by hand, snugging them manually and then using a beam or click-type torque wrench to apply the final torque and confirm the recommended torque value has been reached.
Professional does not recommend using impact guns or torque sticks when installing wheels.
Impact guns deliver torque as torsional impacts, made by internal hammers. Delivering torque as torsional impacts can damage hardware and wheel finish. Some vehicles, such as Porsches, require the use of special sockets to tighten the hardware without damaging their anodized coating.
Torque sticks are designed to limit applied torque by absorbing input torque thru torsion deflection, or twist. However, there are many variables that can affect the torsional deflection (absorbed torque) and the applied (delivered) torque. These can lead to inaccurately applied torque or variations in applied torque.
Some of the variables that can cause inaccurate torque delivery:
Type of impact used (air, electric, cordless)
Power (air pressure, air volume, length of hose, size of fittings, battery power, battery age)
Impacts per second
Size of internal hammers
Possible use of additional adapters
Socket size, weight, length
Operator grip strength
Weight of the impact
Applied angle during use
Attempting to fully tighten hardware with impact guns/torque sticks also prevents using a click-type torque wrench to confirm the specified amount of torque is present. While a click-type torque wrench can identify when the selected torque has been reached, it cannot diagnose excessive torque.
Once you have the right tools, use the appropriate crisscross sequence (patterns shown below) for the number of the vehicle's wheel-attaching hardware positions until all have reached their specified torque value.
New wheels should be re-torqued after the first 50 to 100 driving miles.
This should be done in case the clamping loads have changed following the initial installation due to the metal compression/elongation or thermal stresses affecting the wheels as they are breaking in, as well as to verify the accuracy of the original installation.
When rechecking torque value, wait for the wheels to cool to ambient temperature (never torque a hot wheel). Loosen and retighten to value, in sequence using the torque procedures listed above.
No comments:
Post a Comment